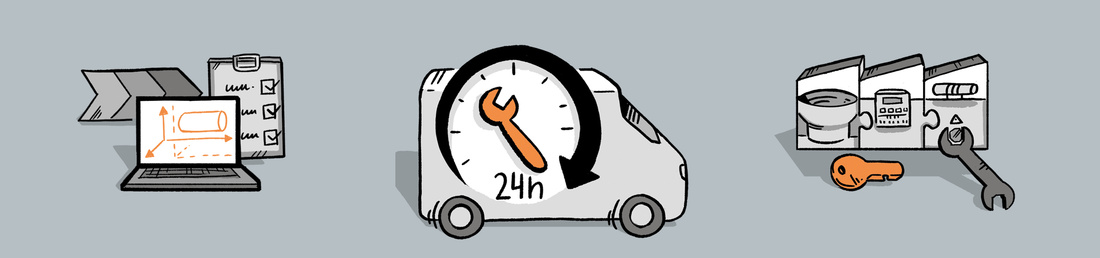
For over 100 years we understand ourselves as a service provider of the industry.
We accompany your inductive processes, starting with the project planning of new plants, through the modification of existing plants up to the recalculation of changed product requirements or geometries.
With our experienced specialists, we are your partner along the production chain, independent of time and place, flexible and reliable.
After commissioning, we look after our customers reliably and flexibly. Starting with the supply of spare parts, the support in the start-up phase to the long-term care in case of repair, everything is done from a single source. Our large warehouse holds numerous components stocked, in case of a plant downtime you can reach us 24/7.
In our laboratory we also heat small and pre-production products for our customers. In this way, prototypes can be made available to the end customer in a timely manner and series maturity can be reached more quickly. Here, too, the heating stages and the development of the inductor production are documented in detail on request.
Our assembly teams work around the clock. On the one hand, we fix disruptions at short notice and ensure production, on the other hand, we support planned repairs, maintenance and modifications. We take over the replacement of burned insulation as well as the complete rewiring of your inductive heating systems. With our converter specialists, we carry out annual maintenance according to the service plan and take over the preventive maintenance. In case of problems with calcified cooling water pipes, we rinse with special acid and replace damaged hose nozzles and sacrificial anodes.
Our assembly vehicles are small moving workshops including the necessary test and measuring equipment. Our fitters are experienced specialists and not tied to a converter manufacturer or type. Regardless of location and time, we are your installation partner and support your maintenance, day, night and weekend. Numerous production companies reduce their own electrical maintenance. Our assembly teams in your factory are also happy to assist with routine tasks and minor repairs.
Our installation partner:
DM - Montage- und Induktionsservice GmbH
Am Hohen Wald 11
42859 Remscheid
Telephone: 0157 83448456
Fax: 0208 56728
E-Mail: info[at]dm-induktion.de
Contact: Erhan Demir
In many cases, customers have functioning facilities that have aged. Through a modification, combined with an exchange or an update of the converters and the inductors, proven processes can be brought to the state of the art without completely renewing the system. In this way you can achieve a significant improvement in the energy balance, combined with an increase in productivity at a fraction of the investment. We are happy to advise and assist you with such modifications or upgrades.
The planning of inductive processes is carried out by us from a single source. On the basis of a specification or a technical task, we determine the effort, calculate the scope of services and determine the appropriate converter based on these values. The converter unit - resonant circuit and inductor are now matched and technically and commercially recorded. On the basis of these principles, we determine the optimized process together with our customers and thus provide a technically sound basis for the design of even complex inductive heating processes. Building on this, we accompany the project through all stages of production to commissioning. In cooperation with experienced partners from special machine construction, the assembly and removal as well as the automated loading or extraction of the components can be included in the project planning.
In cooperation with R & D departments and technical colleges, we develop partnership-based inductive heating processes. In our laboratory, test series up to 100 kW are possible, the inductor production and adaptation takes place synchronously with the development status and is documented in detail. Due to the short distances even complex developments can be handled promptly and flexibly.
The repair of heating coils, furnace coils, transformers and busbars is a focal point of our work. In two fully equipped workshops, 4 teams work on a wide variety of inductive systems. All work is carried out in-house. If an inductor is picked up by our truck, it will first be scrutinized in the incoming inspection. The repair scope is determined in an individual work instruction and the input values of the cooling water and high-voltage test are recorded in a test instruction. On the basis of these documents, we will send a cost estimate to the customer for approval. Subsequently, the repair is carried out, together with the delivery note a test report is sent in which the values of the input and output test are compared. The initial examinations are always carried out in the four - eyes principle.