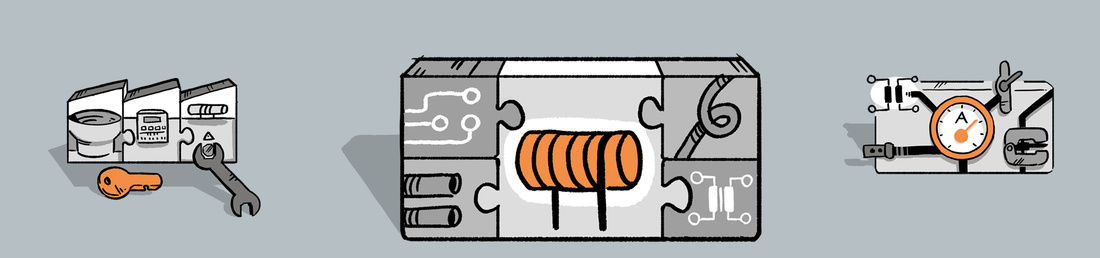
Forming - tempering - hardening - shrinking - melting
With a modern heating coil, the potential applications are nearly endless. As soon as metals get heated, we are in our element. We are your competent partner for the planning of new plants as well as the maintenance and repair of existing plants.
Each job is specially adapted to the workpiece geometry or to the application, so we can only mention a few examples here. Along the inductive process chain, you will receive all spare parts, assemblies and installations from a single source.
In addition to induction technology, we also produce series products made of copper and steel for energy transmission and conveyor technology.
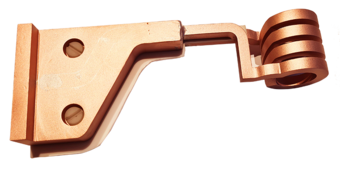
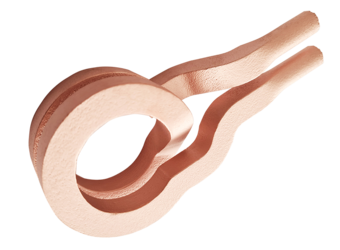

Your Research & Development Partner for the economical production of additively printed heating coils
3D printing of inductors by selective laser sintering - made from 100% pure copper
- 10 years of experience with additively manufactured inductors
- Production according to your drawing or as a development partner - optimized for your process - with adaptation of the surface properties, the material and the geometry, tested in our laboratory ready for installation
The heating coil, the perfect showcase component for additive manufacturing
- any design and filigree geometry can be implemented close to the contour
- 100% reproducible
- short delivery time = reduced storage costs
- low mold and tool costs
- 3D - optimized cooling circuits ensure flow-optimized water cooling
- economical, even with small batch sizes
- no soldering points or welding constrictions on the windings
- Hybrid production combined with milled inductor feet, concentrators and add-on parts
- Long-term tested under 24/7 maximum load, also in soldering/brazing and hardening
- no reflection problems due to the most modern laser quality
- Electrical conductivity: up to 58 MS/m
- Thermal conductivity: 400 ± 15W/(m*K)
- Density: 8,9 g/cm³
Our sales team will be happy to advise you personally on the options. We look forward to your inquiry!
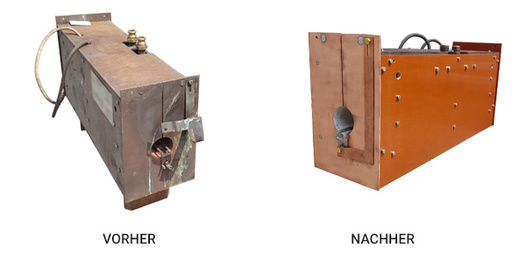
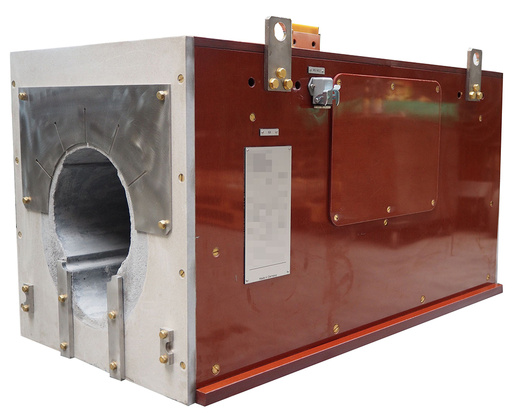
The forge heating coil or billet heater is the first choice of heating in automated forging technology. These heating coils form a focus in our production. In addition to the calculation, development and production of new heating coils, we repair and modify all brands. All necessary work is carried out in our workshops, fast, accurate and reliable. Work and test instructions document every production step.
Advantages that convince:
- constant workpiece temperature
- minimal scale formation
- low wear on the dies
- compact design
- low pre warming times
Together with our customers, we develop, calculate and manufacture the heating coil adapted to the required heating task. In lightweight and heavy construction, with mica or concrete housing, with quick-change devices and inductor frame pre-assembled.
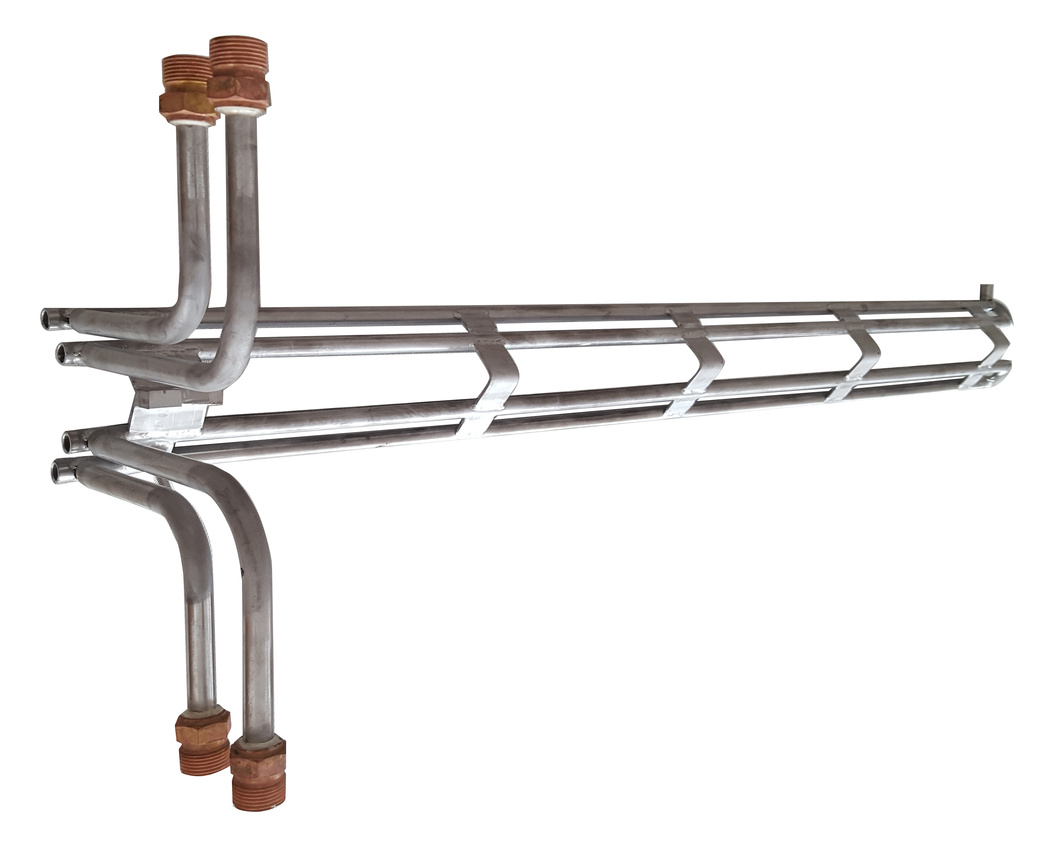
Sliding tubes or material guide tubes form an important element in the production chain. Water-cooled sliding tubes are a major disruptive factor in the event of wear-related leaks, and not infrequently the heating coils or the converter is damaged as well. The sliding tubes are automatically coated in our workshop and delivered ready for installation. After drawing or sample we manufacture for all manufacturers and building types. Upon request, the pipes are drawn and receive a customer - specific order number, so that the replacement part can be reordered easily. The used high - temperature resistant stainless steels are tested batch by batch, each sliding pipe receives a test certificate with pressure test and target - actual water flow rate.
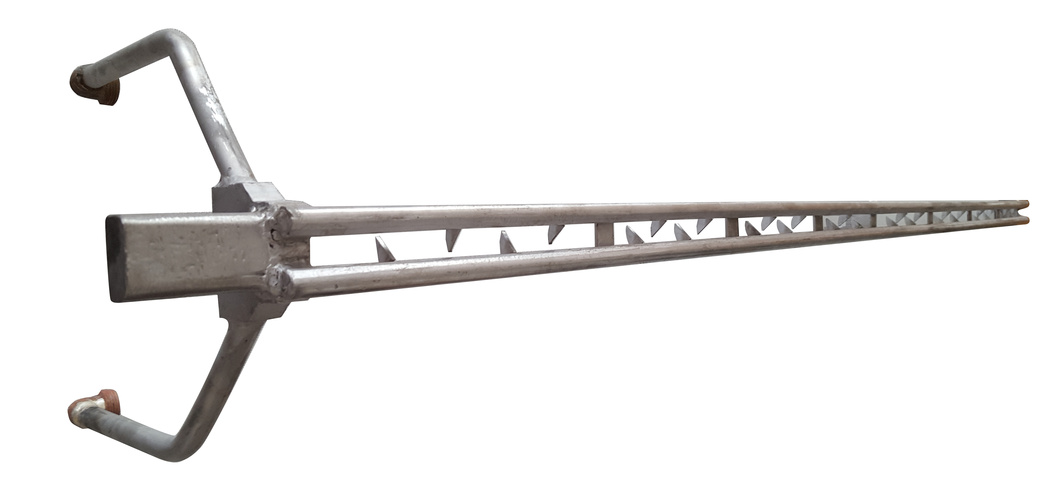
Lifting beams of lift-forged forging plants are subjected to enormous loads. The materials of the milled lifting jacks and the tubes are matched and welded consistently clean. After drawing or sample we manufacture for all manufacturers and building types. Upon request, the lifting bars are drawn and receive a customer-specific order number, so that spare parts procurement is possible without any problems. The high-temperature-resistant stainless steels used are tested in batches, each lifting beam receives a test certificate with pressure test and water flow rate.
Busbars and power water cables form the link between the converter and the heating coil. We develop new systems and repair existing ones. The overhaul of busbars with new cooling ribs made of electrolytic copper and power water cables is carried out by experienced locksmiths in our workshops. We have stocked the usual copper pipes and hose types in stock, so that even short-term repairs can be performed.
The hardening inductor is the core competence in the hardening process. Adapted to the geometry of the component to be hardened, the manufacture of the inductor takes place. On the one hand, the inductor must harmonize with the converter and quench media. On the other hand, a wide variety of materials with diverse designs must be heated homogeneously and reproducibly. The construction of hardening inductors is a matter of experience. We calculate, develop and manufacture hardening inductors from a single source - for over 50 years.
Ring inductors usually form one-winded inductors in copper-blank or coated design. Optionally we equip the inductors with dynamo sheets or fluxtrol to concentrate the magnetic field in certain parts of the workpiece. The heating loop is wound stress-free and soldered with brazing or milled from round copper in one piece. Optionally, ceramic coatings and shielding plates for targeted heat input are possible.
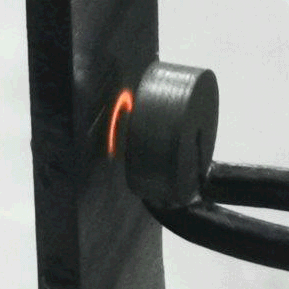
The brazing inductor is the modern way to produce brazing joints safely and homogeneously in reproducible quality. Advantages of the inductive brazing methods are compared to brazing with the flame both in the possibility of automation, as well as by selectively metered heat input with compact brazing inductors difficult to access brazing processes. The inductors look inconspicuous at first glance, but they are exposed to extreme loads. Short circuits due to deformed workpieces and incorrect operation must not cause damage to the brazing peripherals and the converters. Special coatings and the use of concentrators form energy-saving and material-sparing modifications. As a development partner, we manufacture both for the hand-held and for the automated brazing process.
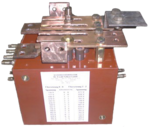
Water-cooled transformers or throttles have long been considered as disposables. However, even in fully encapsulated execution, these are repairable in most cases, at a price that rarely exceeds 50% of the original value. The transformer cores and the potting are renewed, the copper coils prepared as new and possibly partially renewed. During the repair, modifications are carried out, so that a new-value transformer leaves our workshop according to the current state of the art, including a test certificate. In the event of a plant shutdown, we repair on customer request in multi-shift and on weekends.
Fully potted or massively wound, for repair or new production according to drawing or pattern:
- HF transformers
- MF transformers
- Disc transformers
- Deflection transformers (deflection coils)
- DC reactors
- Smoothing reactors
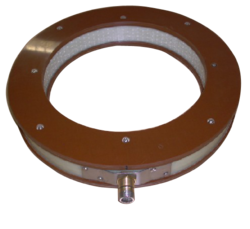
The customer demands for depth of hardness and hardness are subject to ever narrower tolerances. As a result, the choice of hardening temperature and an exact quenching process in automated quenching treatment are becoming more and more critical.
Our new generation of quenching showers combines many advantages:
- The used materials GRP and hard tissue are temperature-resistant, mechanically stable and easy to work with (of course we also manufacture conventional MS-showers on request)
- The construction is multi-part and thus easy to repair
- The purchase is not more expensive than one-piece showers
- The fiberglass middle section combines light construction with enormous durability, even under continuous load

The foundry's water-cooled crucible furnace combines short melting processes with low power losses. We repair, service and produce inductive furnace coils up to 2.5 t. Upon request, our assembly teams disassemble the defective oven, assemble the spare spool and transport the defective oven to our workshop. After the preparation and approval of a cost estimate, we repair professionally and store the spare spool on request. Short reaction times and experienced technicians ensure short downtimes and long service lives. The repair always follows the following pattern:
- Receiving inspection with recording of the actual dimensions
- Determination of the claims expenditure
- Creation of work and test instructions according to DIN ISO
- If a complete repair is required, all components are removed and the copper coil is decoated in a thermal process and annealed in parallel stress-free
- The copper coil is mechanically blasted bare, directed and the target values checked
- The copper coil is isolated according to manufacturer's standard and possibly wound with glass silk tape
- The insulated coil is pressed to the desired height and clamped ready
- Spool tensioners are tested, straightened or renewed and mounted
- If desired, a glass fiber outer sheath for coil protection is introduced
- An initial check is made with inspection of the insulation, the amount of cooling water and a pressure test of the cooling system, as well as all external dimensions and the position of the power - water connections
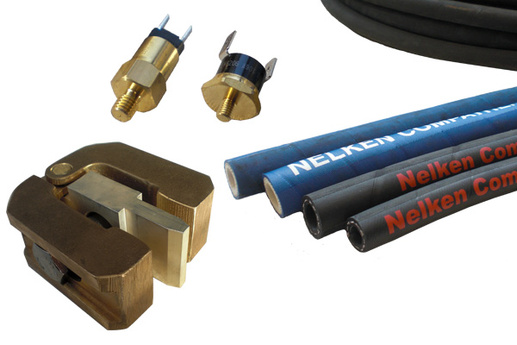
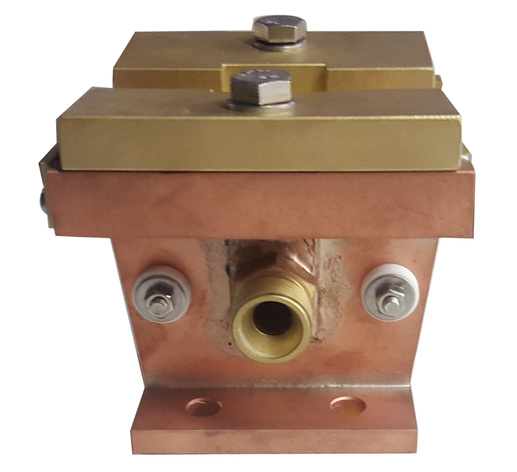
From the copper front plate to the hose clamp made of stainless steel, we supply almost all spare parts in the field of induction technology Below is an overview of our spare parts (in excerpts):
- Electric hoses, electrically non-conductive
- Insulating materials of any kind, high temperature resistant and mechanically stable
- Hose barbs made of brass and stainless steel, also made to pattern
- Stainless steel tubes in almost all sizes
- Copper pipes; round, square or rectangular and special shapes
- NTC sensors in OEM quality
- Temperature sensors of all common manufacturers
- Sacrificial anodes / rod anodes in 3/8 "and ½" incl. MS - grommet
- Inductor clamps, silver-plated design
- Housing panels made of fiberglass or hard tissue, ready for installation or as a sheet product
Mikanit stove protection plate, on request with exchangeable wear ring in the temperature and spray area. In the area of the melting range, one of the most stressed parts is the cover plate. Our Mikanit stove top minimizes rebuild time and maximizes tool life. The principle is based on a double plate, consisting of a lower plate, screwed firmly to the furnace cover plate, and a wear ring with quick-change fitting. All materials are resistant to high temperatures. We manufacture according to your individual melting equipment and supply the wear rings at short notice if required.
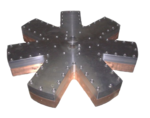
Induction is often used when metals or steel are subjected to special stress and reach their physical limits. For example, when working with a laser or welding sheets, sections can be inductively preheated. Another special application for induction is common practice in the magnetic testing of steel. Here test coils are used in the component negative process with often complicated geometry, which we manufacture for existing systems. For these and many other applications, we supply you with complete solutions, on request incl. converter and recooling system, pre-assembled.
High current technology
The Dr. Ewald Nelken GmbH always works under power to adapt its range of services to the wishes of our customers. In the meantime, our portfolio in the field of high-current technology has grown significantly, so that we can not only offer you air and water-cooled cables and coaxial cables, but also switchgear, switches, contacts, busbars, current bridges, transformers and much more. We are also happy to come to you for maintenance and repair work.
We produce cables with the highest quality standards for a wide variety of applications. Our cables are extremely robust and have a long life and performance. (High-current cables have a complexity that is quickly underestimated, which is why their design and manufacture requires a high degree of know-how.) We offer you the design, manufacture and assembly of custom-made air and water-cooled cables. Our portfolio includes air- or water-cooled coax cables, air-cooled power and grounding straps as well as water-cooled type 4 and type 6 cables for voltages up to 5 KV AC / DC, current loads from 50-250,000 A and up to 500kHz.
Coax cable:
On the basis of tried and tested designs, we develop and manufacture especially low-loss cables, in which the inductive losses in particular are reduced to a minimum. The connections, also rotatable, can be designed according to your wishes and needs. Air cooled up to 3 kA at up to 400 kHz; water-cooled up to 30 kA at up to 400 kHz.
Air-cooled power and grounding straps:
Our air-cooled power and grounding tapes are made solder-free with or without insulation. We offer both foil and fabric versions in copper, usable for length and temperature compensation as well as vibration decoupling. Areas of application are e.g. Energy supply, plant construction, transformer connection or electroplating.
water-cooled single-core cable:
The water-cooled single-core cables that we offer with both pressed and soldered heads are available with a central or ring internal structure (with copper cables). We can offer you a wide variety of designs for your respective applications. These cables are used in induction plant construction but also in general energy supply; Special area: Arc furnace cable; Can be manufactured up to 300 kA and up to 3 kV AC / DC.
We also implement individual solutions. Talk to us, we will advise you.
Please contact our sales department for advice on your individual projects.
Manually or automatically operated contacts in energy systems are exposed to very high loads due to ever higher current densities and mechanical influences, which is why contact systems in our company are subject to constant further development.
We offer fully developed systems for a very large number of application areas, optionally with length or vibration compensation.
Special fields of application are for example:
- stirring coil contacts
- Electroplating → Goods rack systems
Our contact systems are:
- low maintenance
- durable
- customizable
- Thermally resilient
- can be integrated into any automated system control on request
- low wear
- true to size
- Can be designed up to 40,000 amps
We are happy to offer you an individual solution for a manual, mechanical or pneumatic contact system according to your requirements.
Please contact our technicals sales department for advice on your individual projects.
The no-load operated switches we offer are very compact air or water-cooled versions. Its main characteristic is an unmatched power density in the smallest space. The voltage range goes up to max. 3 kV. Usually, switching times of less than 1 second are realized.
Our switches are supplied pneumatically or electrically on the control side. Pneumatically, the operating pressure in the standard case is 4 bar. Electrically, we can offer a voltage range of 24 V to 230 V AC / DC (depending on the model) as standard.
All switches are equipped with auxiliary switches as standard, which report the switch positions and thus allow automation. A personal protection function can be implemented as an option.
As a special service we offer the maintenance and repair of third-party devices.
If this should not be sufficient, we also manufacture replacement devices and components that are compatible with third-party providers in terms of function and connection situation.
We also implement individual solutions. Talk to us, we will advise you.
Please contact our technical sales department for advice on your individual projects.
Our switching devices are characterized by very high robustness under the toughest environmental conditions. Depending on the application, we can design them in air or water-cooled versions. Particularly noteworthy is the low maintenance intensity of our switching devices.
We maintain, repair and manufacture switchgear mainly for the following areas:
- High-current operation: switching devices for currents up to 50 kA at voltages up to 3000 V AC / DC up to 400 kHz
- Railway technology: switching devices for currents up to 30 kA at voltages up to 3 kV AC and 50 Hz
- Medium voltage: switching devices for currents up to 6 kA at voltages up to 36 kV AC / DC and 50/60 Hz
We produce Berg switches, HRW switches, Ferraz, furnace switches, contactors, tap changers and disconnectors, for example; switchable without load or under load; Electromagnetically, motorized or pneumatically driven.
As a service we offer repair, retrofit and production of replacement devices for third-party switching devices.
We also implement individual solutions. Talk to us, we will advise you.
Please contact our sales department for advice on your individual projects.
In addition to our well-known busbars for use in converters, we also offer our customers the individual design and manufacture of their own air- and water-cooled busbar systems. Of course you can also ask us about your existing designs. We manufacture both plugged, welded and screwed systems.
If you have an old system and need spare parts, we would also be happy to recondition components or manufacture almost all makes according to samples. For the special area of energy supply, we offer special solutions for type-tested busbars, e.g. Schneider, Siemens and many more. We also take care of the infeed and outlet boxes.
As a service, we not only equip the plant construction with live components, we also repair or renew such components for the following areas:
- Switchgear for high-current, rail and energy technology
- Air and water-cooled cables from heating and melting systems
- Coil and inductors
- Copper, aluminum and VA welding
- modification of existing systems (high-current technology)
We also implement individual solutions. Talk to us, we will advise you.
Please contact our technical sales department for advice on your individual projects.