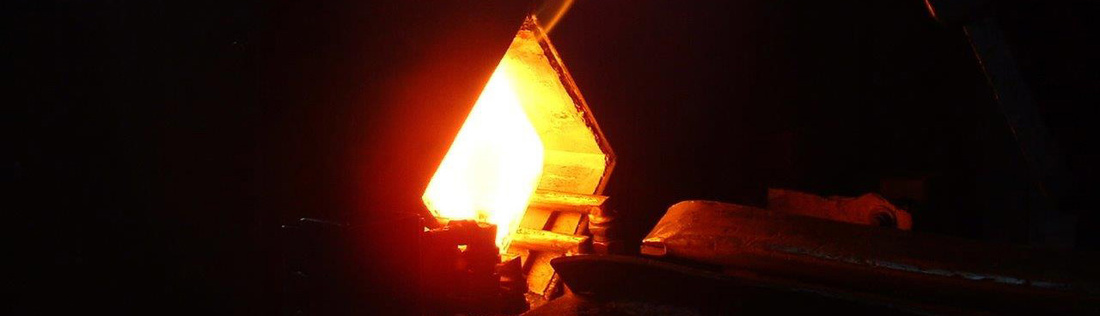
In every industry - in which steel or metals are heated - inductive heating can be used.
In all areas where steel is heated in series, the induction technology offers a reproducible and DIN-testable production, combined with low scaling and optimized energy balance.
The focus is on forging technology, plant engineering, automotive technology and their OEMs, steel and metallurgical plants and hardening shops, as well as the foundry.
In the following industries we act as your full service partner:
In the field of inductive heating we are an experienced partner of plant engineering and mechanical engineering.
Together we develop the process and supply the inductor, on request incl. converter and recooling system.
In After Sale, we supply replacement inductors at short notice and adapt the inductor to new geometries.
Our design has the most common CAD software and can thus incorporate the induction component in complex systems flexibly and ready for installation.
We have been solving the problems of special inductive applications together with our customers for over 50 years and have been looking after numerous automobile manufacturers and their suppliers.
For some years now, in addition to the classic applications of inductive hardening, inductive heat treatment and forging applications, we have also focused on many applications that are specific to electromobility. For example, we are now increasingly dealing with inductive joining processes, automated soldering applications, inductive impregnation or inductive bonding. Due to the high requirements regarding cycle times, limitation of the area to be heated, traceability and repeatability of the processes, inductive heating is perfect for this branch of industry. More information can be found here.
We look after numerous production lines and are your competent and experienced contact for all topics related to inductive heating.
We look at the complex application and deliver the customized, ready-to-install inductive heating unit, with a converter, recooler, feeding and extraction unit on request.
In addition, we maintain and repair existing systems from all manufacturers, flexibly and reliably - at a transparent and performance-oriented fixed price.
We look after the foundry companies with their inductive systems 24/7.
The short-term removal of faults as well as the removal and installation of the smelting furnaces.
The professional repair of defective heating coils and the overhaul of power water cables.
We are happy to store your repaired equipment and deliver on time by our trained installation team.
When re-hosing the converters, we deliver only tested and proven OEM quality.
Numerous hardening shops have inductive hardening plants.
Here we come into play. Adapted to the respective workpiece, we develop and produce the right inductor - optimally matched to the suitable converter.
In addition, we supply complete hardening systems and make preliminary tests in our testing laboratory.
We also carry out the repair of defective inductors and transformers, as well as the maintenance and repair of existing converters of all manufacturers.
The first inductor manufactured by us in 1962 was delivered to a pipe mill and we are traditionally a development partner for many well-known pipe mills.
Regardless of the task, we develop and produce the right inductor, maintain the systems and take over the inductor change.
Burned busbars are overhauled and damaged transformers repaired.
For the inducers of pipe welding lines (line inductors, MF-inductors, etc.) we have all components and spare parts for short-term repair in stock.
Induction heating systems are the first choice in the forging industry with series products.
Regardless of the manufacturer, we develop, maintain, repair and produce heating coils of all power classes and sizes.
From the calculation of new geometries to the modification and optimization of the energy balance, you receive the full service from a single source.
From billet- and bar heating to pipe heating, we are your competent partner.
Steel mills and rolling mills operate numerous induction systems, both in terms of tempering and strip heating in the hot rolling mill.
We supply tunnel coils and C-inductors and the classic rod heaters to this industry.
We support the electrical repair with our assembly teams and supply various spare parts.
From history, we manufacture multi-point contact pantographs and crane runner expansion joints for the crane plants of the steelworks and undertake the manufacture of special components made of steel, copper or brass.
The wind power industry and the manufacturers of large engines have one thing in common: everything is a bit bigger.
In this industry, we are both advisory in the development of hardening processes and their implementation.
In addition, we manufacture and repair very large inductors with a housing made of a highly heat-resistant and particularly stable special ceramic or a housing made of mica or fiberglass.